Regular maintenance of gantry milling machines is a very important measure
The development of gantry milling machines has been highly valued for its injection of acceleration concepts. The widely used transmission components such as electric spindles, linear motors, and linear guides that provide technical support for high-speed operation have pushed the operating speed of machine tools to new heights. The innovative planning of the spindle replaceable horizontal boring and milling machining center addresses the advantages and disadvantages of both the electric spindle and the movable telescopic structure of the boring bar. It has the effect of composite processing and dual use of one machine, and is also a major feature of gantry milling machines.
Regular maintenance method for gantry milling machine:
1. Clean the smooth oil pool inside the bed, lifting platform, and workbench base every 3 months, and clean the oil net of the smooth oil pump with gasoline at least twice a year.
2. The lifting screw is polished with aluminum disulfide oil every two months.
3. Adjustment of gaps in various parts of the machine tool:
(1) Smooth adjustment of the spindle requires one drop of oil to pass through every minute.
(2) The adjustment of the longitudinal lead screw transmission gap on the workbench should be made every 3 months or according to practical use. The requirement is that the transmission gap should be fully reduced, and the gap of the lead screw should not exceed 1/40 turn. At the same time, there should be no jamming phenomenon on the entire length.
(3) The adjustment of the axial clearance of the vertical lead screw in the work is intended to reduce the transmission clearance between the lead screw and the nut, while also minimizing the cooperation clearance between the lead screw and the workbench in the axial direction.
(4) Adjust the radial clearance of the spindle bearing according to practical usage.
4. Adjustment requirements for the workbench moving clutch
(1) When the conflict clutch is disengaged, the total gap between the conflict discs should not be less than 2-3mm.
(2) When the conflict clutch is closed, the conflict plate should be tightly pressed, and the iron core of the electromagnet should be tightened. If the iron core of the electromagnet cooperates correctly, the electromagnet will not make any noise during the tightening state.
Regular maintenance of gantry milling machine
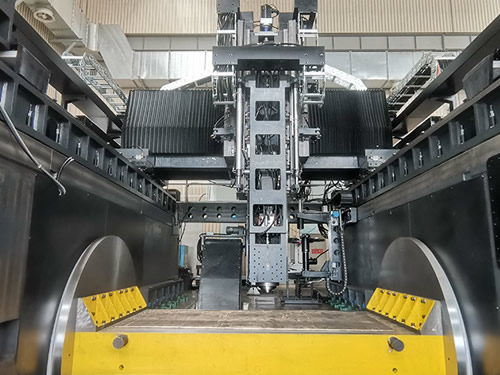
26
Oct